The size distribution of raw sand particles significantly affects the quality of castings. When using coarser grit, molten metal tends to seep into the core grit, resulting in a poor casting surface. The use of finer sand can produce a better and smoother casting surface, but requires a higher amount of binder, and at the same time reduces the air permeability of the core, which may cause casting defects. In general sand casting process, especially when silica sand is used, the raw sand is generally within the following size range:
Average fineness 50–60 AFS (average particle size 220–250 μm): better surface quality and lower binder usage
Fine powder (less than 200 mesh) content ≤2%: can reduce the amount of binder
Mud content (particle content less than 0.02mm) ≤0.5%: can reduce the amount of binder
Particle size distribution: 95% of the sand is concentrated on the 4th or 5th sieve: easy to compact and reduce swelling defects
Air permeability of dry sand: 100-150: reduce pore defects
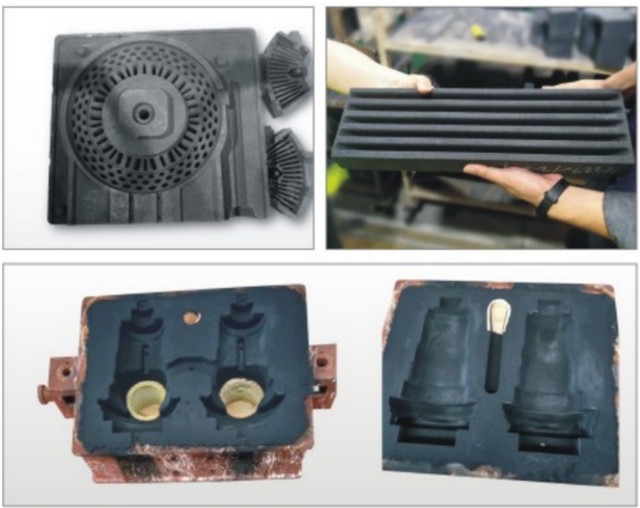
Ceramic sand, due to its nearly round particle shape, excellent fluidity, high air permeability, and the characteristics of wide particle size distribution and single-mesh combination mixing in the production process, in casting practice, in addition to following the above common characteristics, there are Its own unique gradation characteristics make it free from segregation and delamination during transportation and transportation; it has good wet strength in the application of green mold sand and no-bake resin sand. For the sand casting process using binders, the use of multi-sieve distribution makes smaller particles fill in the gaps between larger particles and inlay each other, increasing the "connecting bridge" of the binder, thereby improving the bond strength of the core, etc. It is an effective way.
Summarizing the application of ceramic sand for more than 20 years, the particle size requirements and distribution of ceramic sand used in different casting processes are roughly listed as follows:
● RCS (Resin Coated Ceramic Sand)
AFS values of 50-70, 70-90, and 90-110 are all used, distributed in 4 or 5 sieves, and the concentration is above 85%;
● No-bake resin sand
(Including furan, alkali phenolic, PEP, Bonnie, etc.): AFS 30-65 are used, 4 sieves or 5 sieves distribution, the concentration is over 80%;
● Lost Foam Process/Lost Weight Foundry Process
10/20 mesh and 20/30 mesh are more commonly used, which can improve air permeability, ensure the recycling rate of ceramic sand after pouring, and reduce consumption;
● Cold Box Sand Process
AFS 40-60 is more commonly used, distributed with 4 or 5 sieves, and the concentration is above 85%;
● 3D Sand Printing
2 sieves are distributed, up to 3 sieves, with a concentration of more than 90%, ensuring a uniform sand layer thickness. The average fineness is widely distributed according to different uses
Post time: Mar-27-2023